When you think of manufacturing you probably envision buildings with machines that are huge. But in this nondescript Chicago storefront a revolution is transforming the American factory — with very different kinds of machines.
3DPX is a 3D printing company making thousands of different parts each year out of plastic and metal. It's called additive manufacturing, and 3D printing is the main technology.
CEO of 3DPX Chris Martinez gave us a tour of his company, their machines, and their office mascot.
SCRIPPS NEWS' LAUREN MAGARINO: Additive printing and manufacturing. What exactly does that mean?
CHRIS MARTINEZ: There was always this analog traditional manufacturing, where you had this mold and you pushed plastic into it. Or you take big blocks of plastic or metal and you machine or grind it away. Additive is just building parts from nothing, right in powder and plastic, all different types of substrates.
"We’re headed to the main printer room. We do all laser sintering. It’s all a powder based process. Think of building a loaf of bread out of its slices," Martinez said. "The temperature in this room – it’s really hot. It smells like you walked into a printing shop."
Within these machines hangs a bin of fine plastic powder. The computer guides a laser that shoots down, gluing or sintering together the plastic on the top layer. After one layer is sintered, the bin lowers slightly, and a roller lays down the next layer of powder. Then the laser sinters together the next layer, building the item from the bottom up. When it's done an employee then sifts through the powder to find the piece that was printed, cleans the powder off and the item is ready.
To 3D print metal parts, the process is similar, but instead of plastic the machines use metal powder. And instead of blasting it with a laser, the machine deposits layers of a glue, called a binder, to form the metal shape. 3DPX makes everything from parts for racing cars to architectural models, but its main customers are medical device companies.
"We do a lot of dental applications, surgical guides. It’s a biocompatible material, and now it’s accepted by insurance, so it’s really taking off," Martinez said.
Additive manufacturing is changing how companies make almost everything. NASA uses 3D printing to create a metallic fabric.
Companies like Alquist are 3D printing buildings from the ground up. 3D printing could even allow astronauts to make specialized parts in space. Scientists at Washington State University printed these parts using simulated martian dust, mixed with titanium.
And citizens are 3D printing unregistered, so-called ghost guns without serial numbers, some which can evade metal detectors. Several federal agencies and us states have passed regulations or bans on 3d printed guns
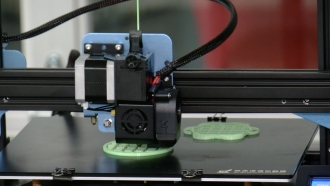
3D Printing Helps Fill A Need For More Protective Masks
The coronavirus has strained resources for health care workers. But 3D printing may be one way to help close the gap.
MAGARINO: Has 3D printing revolutionized manufacturing?
MARTINEZ: The pandemic kind of amplified it where it's this decentralized manufacturing. Businesses are scared of this long supply chain. And so they want to buy closer and they don't want to hold all this inventory. And so 3D printing facilitates that. Certainly here in the states and our cities, it's we have lots of customers that are just a few miles away versus going all the way overseas. Being able to iterate quickly is is a key component to developing any product, consumer products, medical products. And so using additive, we can have designs changed, produced and shipped in days versus weeks or months. And so bringing a product to market, it can happen in a very short amount of time. The demand is increasing faster than the companies are building and creating these facilities. And so this is going to happen for the next five, 10, 15 years. And, you know, we're just happy to be able to facilitate it, you know, and obviously it requires skilled labor and that's just a shifting workforce. It's not eliminating jobs through automation. It's creating skilled labor that is able to utilize and run the automation.
MAGARINO: What kind of skills are needed to do this work?
MARTINEZ: For example here all all walks of life from master's degrees with engineering to people that have been in manufacturing for a while, fresh out of college, haven't gone to college, it's just able to learn it on demand as well, especially because it's such a new technology. Everybody's learning it.
MAGARINO: There are some folks who may say, hey, all this plastic.
MARTINEZ: So this mass manufacturing of thousands and thousands of parts, we're moving away from it. And so, yes, we will produce plastic parts, but it's at such a smaller quantity. And so this waste doesn't exist. We don't have to over create. It's just on demand.
MAGARINO: How does 3D printing scale? What does that journey look like for the industry?
MARTINEZ: There's this institutional knowledge that things have to be done the certain way, traditional manufacturing. And it's when the students come out of college and they think differently about design, about manufacturing, and they break down those assumptions. That adoption really has legs now.